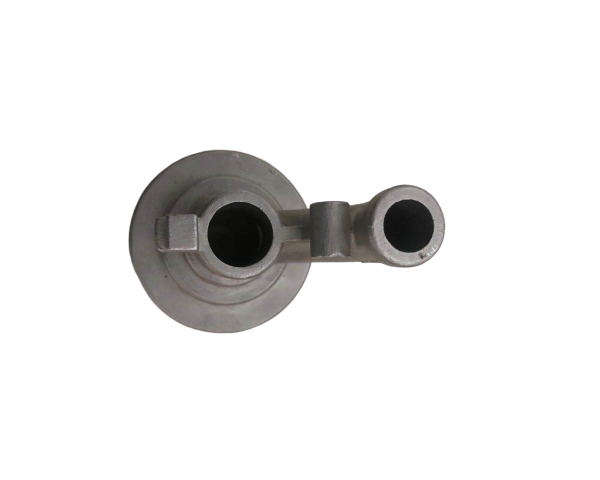
不锈钢精密铸件
压铸件是一种压力铸造的零件,是使用装好铸件模具的压力铸造机械压铸机,将加热为液态的铜、锌、铝或铝合金等金属浇入压铸机的入料口,经压铸机压铸,铸造出模具限制的形状和尺寸的铜、锌、铝零件或铝合金零件,这样的零件通常就被叫做压铸件。压铸件在不同的地方有不同的叫法,如压铸零件、压力铸件、压铸件、压铸铝、压铸锌件、压铸铜件、铜压铸件、锌压铸件、铝压铸件铝压铸件、铝压合金铸件、铝合金压铸零件等。
中文名:压铸件
外文名:pressure casting
限 制:形状和尺寸
特 点:很好的流动性和可塑性
别 称:压铸零件、压力铸件等
原 料:铜、锌、铝或铝合金等
特性:
由于金属铜、锌、铝及铝合金具有很好的流动性和可塑性,而且铸造加工是在有压力的压铸机中铸造,因此铝压铸件可以做出各种较复杂的形状,也可作出较高的精度和光洁度,从而很大程度的减少了铸件的机械加工量和金属铜、锌、铝或铝合金的铸造余量,不仅节约了电力、金属材料、还大大节约了劳动成本;而铜、锌、铝及铝合金具有优良的导热性,较小的比重和高可加工性;从而压铸件被广泛应用于汽车制造、内燃机生产、摩托车制造、电动机制造、油泵制造、传动机械制造、精密仪器、园林美化、电力建设、建筑装饰等各个行业。
应用:
压铸件可以被制造为压铸汽车配件、压铸汽车发动机管件、压铸空调配件、压铸汽油机气缸缸盖、压铸气门摇臂、压铸气门支座、铸电力配件、压铸电机端盖、压铸壳体、压铸泵壳体、压铸建筑配件、压铸装饰配件、压铸护栏配件、压铸轮等等零件,随着国内制造装备业发展水平的不断提高,压铸机的装备水平也显著提高,可以制造的零件种类也在不断得到扩大,压铸出来的零件的精度、零件的复杂程度也得到了较大的提升,相信在不远的将来,压铸件会更好的服务于我们的生产和生活的!
缺陷:
流痕
其他名称:条纹。
特征:铸件表面上呈现与金属液流动方向相一致的,用手感觉得出的局部下陷光滑纹路。此缺陷无发展方向,用抛光法能去除。
产生原因:
1、两股金属流不同步充满型腔而留下的痕迹。
2、模具温度低,如锌合金模温低于150℃,铝合金模温低于180℃,都易产生这类缺陷。
3、填充速度太高。
4、涂料用量过多。
排除措施:
1、调整内浇口截面积或位置。
2、调整模具温度,增大溢流槽。
3、适当调整填充速度以改变金属液填充型腔的流态。
4、涂料使用薄而均匀。
冷隔水纹
其他名称:冷接(对接),水纹。
特征:温度较低的金属流互相对接但未熔合而出现的缝隙,呈不规则的线形,有穿透的和不穿透的两种,在外力的作用下有发展的趋势。
产生原因:
1、金属液浇注温度低或模具温度低。
2、合金成分不符合标准,流动性差。
3、金属液分股填充,熔合不良。
4、浇口不合理,流程太长。
5、填充速度低或排气不良。
6、比压偏低。
排除措施:
1、适当提高浇注温度和模具温度。
2、改变合金成分,提高流动性。
3、改进浇注系统,加大内浇口速度,改善填充条件。
4、改善排溢条件,增大溢流量。
5、提高压射速度,改善排气条件。
6、提高比压。
擦伤
其他名称:拉力、拉痕、粘模伤痕。
特征:顺着脱模方向,由于金属粘附,模具制造斜度太小而造成铸件表面的拉伤痕迹,严重时成为拉伤面。
产生原因:
1、型芯、型壁的铸造斜度太小或出现倒斜度。
2、型芯、型壁有压伤痕。
3、合金粘附模具。
4、铸件顶出偏斜,或型芯轴线偏斜。
5、型壁表面粗糙。
6、涂料常喷涂不到。
7、铝合金中含铁量低于0.6%。
排除措施:
1、修正模具,保证制造斜度。
2、打光压痕。
3、合理设计浇注系统,避免金属流对冲型芯、型壁,适当降低填充速度。
4、修正模具结构。
5、打光表面。
6、涂料用量薄而均匀,不能漏喷涂料。
7、适当增加含铁量至0.6~0.8%。
凹陷
其他名称:缩凹、缩陷、憋气、塌边。
特征:铸件平滑表面上出现的凹瘪的部分,其表面呈自然冷却状态。
产生原因:
1、铸件结构设计不合理,有局部厚实部位,产生热节。
2、合金收缩率大。
3、内浇口截面积太小。
4、比压低。
5、模具温度太高。
排除措施:
1、改善铸件结构,使壁厚稍为均匀,厚薄相差较大的连接处应逐步缓和过渡,消除热节。
2、选择收缩率小的合金。
3、正确设置浇注系统,适当加大内浇口的截面积。
4、增大压射力。
5、适当调整模具热平衡条件,采用温控装置以及冷却等。
气泡
其他名称:鼓泡。
特征:铸件表皮下,聚集气体鼓胀所形成的泡。
产生原因:
1、模具温度太高。
2、填充速度太高,金属流卷入气体过多。
3、涂料发气量大,用量过多,浇注前未燃尽,使挥发气体被包在铸件表层。
4、排气不顺。
5、开模过早。
6、合金熔炼温度过高。
排除措施:
1、冷却模具至工作温度。
2、降低压射速度,避免涡流包气。
3、选用发气量小的涂料,用量薄而均匀,燃尽后合模。
4、清理和增设溢流槽和排气道。
5、调整留模时间。
6、修整熔炼工艺。
气孔
其他名称:空气孔、气眼。
特征:卷入压铸件内部的气体所形成的形状较为规则,表面较为光滑的孔洞。
产生原因:主要是包卷气体引起:
1、浇口位置选择和导流形状不当,导致金属液进入型腔产生正面撞击和产生旋涡。
2、浇道形状设计不良。
3、压室充满度不够。
4、内浇口速度太高,产生湍流。
5、排气不畅。
6、模具型腔位置太深。
7、涂料过多,填充前未燃尽。
8、炉料不干净,精炼不良。
9、机械加工余量太大。
排除措施:
1、选择有利于型腔内气体排除的浇口位置和导流形状,避免金属液先封闭分型面上的排溢系统。
2、直浇道的喷嘴截面积应尽可能比内浇口截面积大。
3、提高压室充满度,尽可能选用较小的压室并采用定量浇注。
4、在满足成型良好的条件下,增大内浇口厚度以降低填充速度。
5、在型腔最后填充部位处开设溢流槽和排气道,并应避免溢流槽和排气道被金属液封闭。
6、深腔处开设排气塞,采用镶拼形式增加排气。
7、涂料用量薄而均匀,燃尽后填充,采用发气量小的涂料。
8、炉料必须处理干净、干燥,严格遵守熔炼工艺。
9、调整压射速度,慢压射速度和快压射速度的转换点。
10、降低浇注温度,增加比压。
缩孔
其他名称:缩眼、缩空。
特征:压铸件在冷凝过程中,由于内部补偿不足所造成的形状不规则,表面较粗糙的孔洞。
产生原因:
1、合金浇注温度过高。
2、铸件结构壁厚不均匀,产生热节。
3、比压太低。
4、溢流槽容量不够,溢口太薄。
5、压室充满度太小,余料(料饼)太薄,最终补缩起不到作用。
6、内浇口较小。
7、模具的局部温度偏高。
排除措施:
1、遵守合金熔炼规范,合金液过热时间太长,降低浇注温度。
2、改进铸件结构,消除金属积聚部位,均匀壁厚,缓慢过渡。
3、适当提高比压。
4、加大溢流槽容量,增厚溢流口。
5、提高压室充满度,采用定量浇注。
6、适当改善浇注系统,以利压力很好地传递。
花纹
特征:铸件表面上呈现的光滑条纹,肉眼可见,但用手感觉不出的,颜色不同于基体金属的纹络,用0#砂布 稍擦几下即可去除。
产生原因:
1、填充速度太快。
2、涂料用量太多。
3、模具温度偏低。
排除措施:
1、尽可能降低压射速度。
2、涂料用量薄而均匀。
3、提高模具温度。
裂纹
特征:铸件上合金基体被破坏或断开形成细丝状的缝隙,有穿透的和不穿透的两种,有发展的趋势。
裂纹可分为冷裂纹和热裂纹两种,它们的主要区别是:冷裂纹铸件开裂处金属未被氧化,热裂纹铸件开裂处 金属被氧化。
产生原因:
1、铸件结构不合理,收缩受到阻碍,铸件圆角太小。
2、抽芯及顶出装置在工作中发生偏斜,受力不均匀。
3、模具温度低。
4、开模及抽芯时间太迟。
5、选用合金不当或有害杂质过高,使合金塑性下降。锌合金:铅、锡、镉、铁偏高铝合金:锌、铜、铁偏高 铜合金:锌、硅偏高镁合金:铝、硅、铁偏高。
排除措施:
1、改进铸件结构,减少壁厚差,增大铸造圆角。
2、修正模具结构。
3、提高模具工作温度。
4、缩短开模及抽芯时间。
5、严格控制有害杂质,调整合金成份,遵守合金熔炼规范或重新选择合金pai号。
欠铸
其他名称:浇不足、轮廓不清、边角残缺。
特征:金属液未充满型腔,铸件上出现填充不完整的部位。
产生原因:
1、合金流动不良引起:
(1)金属液含气量高,氧化严重,以致流动性下降。
(2)合金浇注温度及模具温度过低。
(3)内浇口速度过低。
(4)蓄能器内氮气压力不足。
(5)压室充满度低。
(6)铸件壁太薄或厚薄悬殊等设计不当。
2、浇注系统不良引起:
(1)浇口位置、导流方式、内浇口股数选择不当。
(2)内浇口截面积太小。
3、排气条件不良引起:
(1)排气不畅。
(2)涂料过多,未被烘干燃尽。
(3)模具温度过高,型腔内气体压力较高,不易排出。
排除措施:
1、改善合金的流动性:
(1)采用正确的熔炼工艺,排除气体及非金属夹杂物。
(2)适当提高合金浇注温度和模具温度。
(3)提高压射速度。
(4)补充氮气,提高有效压力。
(5)采用定量浇注。
(6)改进铸件结构,适当调整壁厚。
2、改进浇注系统:
(1)正确选择浇口位置和导流方式,对非良形状铸件及大铸件采用多股内浇口为有利。
(2)增大内浇口截面积或提高压射速度。3、改善排气条件:
(1)增设溢流槽和排气道,深凹型腔处可开设通气塞。
(2)涂料使用薄而均匀,吹干燃尽后合模。
(3)降低模具温度至工作温度。
印痕
其他名称:推杆印痕、镶块或活动块拼接印痕。
特征:铸件表面由于模具型腔磕碰及推杆、镶块、活动块等零件拼接所留下的凸出和凹下的痕迹。
产生原因:
1、推杆调整不齐或端部磨损。
2、模具型腔、滑块拼接部分和其活动部分配合欠佳。
3、推杆面积太小。
排除措施:
1、调整推杆至正确位置。
2、紧固镶块或其他活动部分,消除不应有的凹凸部分。
3、加大推杆面积或增加个数。
网状毛刺
其他名称:网状痕迹、网状花纹、龟裂毛刺。
特征:由于模具型腔表面产生热疲劳而形成的铸件表面上的网状凸起痕迹和金属刺。
产生原因:
1、模具型腔表面龟裂造成的痕迹,内浇口区域附近的热传导最集中,摩擦阻力最大,经受熔融金属的冲蚀最 强,冷热交变最剧,最易产生热裂,形成龟裂。
2、模具材料不当或热处理工艺不正确。
3、模具冷热温差变化大。
4、合金液浇注温度过高,模具预热不够。
5、模具型腔表面粗糙度Ra太大。
6、金属流速过高及正面冲刷型壁。
排除措施:
1、正确选用模具材料及合理的热处理工艺。
2、模具在压铸前必须预热到工作温度范围。
3、尽可能降低合金浇注温度。
4、提高模具型腔表面质量,降低Ra数值。
5、镶块定期退火,消除应力。
6、正确设计浇注系统,在满足成型良好的条件下,尽可能用较小的压射速度。
有色斑点
其他名称:油斑、黑色斑点。
特征:铸件表面上呈现的不同于基体金属的斑点,一般由涂料碳化物形成。
产生原因:
1、涂料不纯或用量过多。
2、涂料中含石墨过多。
排除措施:
1、涂料使用应薄而均匀,不能堆积,要用压缩空气吹散。
2、减少涂料中的石墨含量或选用无石墨水基涂料。
麻面
特征:充型过程中由于模具温度或合金液温度太低,在近似于欠压条件下铸件表面形成的细小麻点状分布区 域。
产生原因:
1、填充时金属分散成密集液滴,高速撞击型壁。
2、内浇口厚度偏小。
排除措施:
1、正确设计浇注系统,避免金属液产生喷溅,改善排气条件,避免液流卷入过多气体,降低内浇口速度并提 高模具温度。
2、适当调整内浇口厚度。
飞边
其他名称:披缝。
特征:铸件边缘上出现的金属薄片。
产生原因:
1、压射前机器的锁模力调整不佳。
2、模具及滑块损坏,闭锁元件失效。
3、模具镶块及滑块磨损。
4、模具强度不够造成变形。
5、分型面上杂物未清理干净
6、投影面积计算不正确,超过锁模力。
7、压射速度过高,形成压力冲击峰过高。
排除措施:
1、检查合模力或增压情况,调整压射增压机构,使压射增压峰值降低。
2、检查模具滑块损坏程度并修整,确保闭锁元件起到作用。
3、检查磨损情况并修复。
4、正确计算模具强度。
5、清除分型面上的杂物。
6、正确计算调整锁模力。
7、适当调整压射速度。
分层
其他名称:隔皮。
特征:铸件上局部存在有明显的金属层次。
产生原因:
1、模具刚性不够,在金属液填充过程中,模板产生抖动。
2、压室冲头与压室配合不好,在压射中前进速度不平稳。
3、浇注系统设计不当。
排除措施:
1、加强模具刚度,紧固模具部件。
2、调整压射冲头与压室,保证配合良好。
3、合理设计内浇口。
疏松
特征:铸件表层上呈现松散不紧实的宏观组织。
产生原因:
1、模具温度过低。
2、合金浇注温度过低。
3、比压小。
4、涂料过多。
排除措施:
1、提高模具温度至工作温度。
2、适当提高合金浇注温度。
3、提高比压。
4、涂料薄而均匀。
错边错扣
其他名称:错缝。
特征:铸件的一部分与另一部分在分型面上错开,发生相对位移(对螺纹称错扣)。
产生原因:
1、模具镶块位移。
2、模具导向件磨损。
3、两半模的镶块制造误差。
排除措施:
1、调整镶块,加以紧固。
2、更换导柱导套。
3、进行修整,消除误差。
变形
其他名称:扭曲、翘曲。
特征:铸件的几何形状与设计要求不符的整体变形。
产生原因:
1、铸件结构设计不良,引起不均匀的收缩。
2、开模过早,铸件刚性不够。
3、铸造斜度太小。
4、取置铸件的操作不当。
5、推杆位置布置不当。
排除措施:
1、改进铸件结构,使壁厚均匀。
2、确定最佳开模时间,加强铸件刚性。
3、放大铸造斜度。
4、取放铸件应小心,轻取轻放。
5、铸件的堆放应用专用箱,去除浇口方法应恰当。
6、有的变形铸件可经整形消除。
碰伤
特征:铸件表面因碰击而造成的伤痕。
产生原因:
1、去浇口、清理、校正和搬运流转过程中不小心碰伤。
排除措施:
1、清理铸件要小心,存放及运输铸件,不应堆叠或互相碰击,采用专用存放运输运输箱。
硬质点
其他名称:氧化夹杂、夹渣。
特征:铸件基体内存在有硬度高于金属基体的细小质点或块状物,使加工困难,刀具磨损严重,加工后铸件 上常常显示出不同亮度的硬质点。
产生原因:合金中混入或析出比基体金属硬的金属或非金属物质,如AL2O3及游离硅等。
1、氧化铝(AL2O3):
(1)铝合金未精练好。
(2)浇注时混入了氧化物。
2、由铝、铁、锰、硅组成的复杂化合物,主要上由MnAL3在熔池较冷处形成,然后以MnAL3为核心使Fe析出, 又有硅等参加反应形成化合物。
3、游离硅混入物:
(1)铝硅合金含硅量高。
(2)铝硅合金在半液态浇注,存在了游离硅。
排除措施:
1、熔炼时要减少不必要的搅动和过热,保持合金液的纯净,铝合金液长期在炉内保温时,应周期性精炼去 气。
2、铝合金中含有钛、锰、铁等组元时,应勿使偏析并保持洁净,用干燥的精炼剂精炼,但在铝合金含有镁 时,要注意补偿。
3、铝合金中含铜、铁量多时,应使含硅量降低到10.5%以下,适当提高浇注温度以先使硅析出。
脆性
特征:铸件基本金属晶粒过于粗大或细小,使铸件易断裂或碰碎。
产生原因:
1、合金液过热过大或保温时间过长。
2、激烈过冷,结晶过细。
3、铝合金中杂质锌、铁等含量太多。
4、铝合金中含铜量超出规定范围。
排除措施:
1、合金不宜过热,避免合金长时间保温。
2、提高模具温度,降低浇注温度。
3、严格控制合金化学成分。
4、保持坩埚涂料层完整良好。
渗漏
特征:压铸件经试验产生漏水、漏气或渗水。
产生原因:
1、压力不足。
2、浇注系统设计不合理或铸件结构不合理。
3、合金选择不当。
4、排气不良。
排除措施:
1、提高比压。
2、改进浇注系统和排气系统。
3、选用良好合金。
4、尽量避免加工。
5、铸件进行浸渍处理。
杂质
特征:经化学分析,铸件合金元素不符要求或杂质太多。
产生原因:
1、配料不正确。
2、原材料及回炉料未加分析即行投入使用。
排除措施:
1、炉料应经化学分析后才能配用。
2、炉料应严格管理,新旧料要按一定比例配用。
3、严格遵守熔炼工艺。
4、熔炼工具应刷涂料。
强度
特征:铸件合金的机械强度、延伸率低于要求标准。
产生原因:
1、合金化学成分不符标准。
2、铸件内部有气孔、缩孔、夹渣等。
3、对试样处理方法不对等。
4、铸件结构不合理,限制了铸件达到标准。
5、熔炼工艺不当。
排除措施:
1、配料熔化要严格控制化学成分及杂质含量。
2、严格遵守熔炼工艺。
3、按要求做试样,在生产中要定期对铸件进行工艺性试验。
4、严格控制合金熔炼温度和浇注温度,尽量消除合金形成氧化物的各种因素。
发展前景:
我国经济保持着高速发展的势头。由于资源与环境的矛盾日益激化,根据科学发展观的要求,循环经济和清洁生产已成为社会经济可持续发展的重要国策。专家指出,压铸范畴,即包括低压铸造和挤压铸造等各种压力下有色金属铸造成型工艺,其总产量约为150万吨。
据了解,全国汽车总产量达到728万辆,同比增长27.6%,其中轿车产量387万辆,同比增长39.7%。2012年,全国压铸件总产量1024000吨,其中:铝压铸件802140吨、镁压铸件13620吨。2012年1-10月份,全国轿车产量385.01万辆,同比增长23.4%;销售360.01万辆,同比增长22.0%。压铸市场仍将保持快速增长势态。压铸有色金属资源可循环利用和压铸少无切削工艺的先进性,特别适应循环经济和清洁生产的要求,符合国家经济发展总方针。汽车轻量化,更加速了铝镁压铸件市场的发展;国际有色金属压铸件生产重心向我国转移已成必然趋势,压铸市场发展空间巨大。
铝合金压铸件需求增大 促进压铸件产业发展
汽车产业是国内压铸件产业的重要客户之一。随着国内经济的发展和人民生活水平的提高,国内汽车销量直线上升,这就在很大程度上推动了国内压铸件产业,尤其是铝合金压铸件产业的发展。随着国内汽车轻量化呼声的越来越高,汽车行业内部的优化升级也在逐渐落实,逐步用铝铸件代替灰铁铸件,这就刺激了对铝合金压铸件的需求量不断高涨。另外,随着全球的压铸产业发展非常迅猛,各行各业对铝合金压铸件的需求量也在不断增大,压铸件产业的发展前景很广阔。
质量:
压铸模具表面温度的控制对生产高质量的压铸件来说,是非常重要的。不平均或不适当的模具温度亦会导致铸件尺寸不稳定,在生产过程中顶出铸件变形,产生热压力、粘模、表面凹陷、内缩孔及热泡等缺陷。模温差异较大时,对生产周期中的变量,如填充时间、冷却时间及喷涂时间等产生不同程度的影响。
产量:
2012年,全国压铸件总产量1024000吨,其中铝压铸件802140吨、镁压铸件13620吨。
常见问题:
压铸件部分未成形,型腔充不满
产生原因:
1、压铸模温度太低;
2、金属液温度低;
3、压机压力太小;
4、金属液不足;压射速度太高;
5、空气排不出来。
调整方法:
1- 2、提高压铸模,金属液温度;
3、更换大压力压铸机;
4、加足够的金属液,减小压射速度,加大进料口厚度。
设计规范:
压铸件的设计一定要考虑到压铸件壁厚、压铸件铸造圆角和脱模斜度、加强筋、压铸件上铸孔和孔到边缘的最小距离、压铸件上的长方形孔和槽、压铸件内的嵌件、压铸件的加工余量七个方面 [1] 。
铸造圆角设计规范
通常压铸件各个部分相交应有圆角(分型面处除外),可使金属填充时流动平稳,气体也较容易排出,并可避免因锐角而产生裂纹。对于需要进行电镀和涂饰的压铸件,圆角可以均匀镀层,防止尖角处涂料堆积。压铸件的圆角半径R一般不宜小于1mm,最小圆角半径为0.5 mm。
压铸件内的嵌件设计规范
首先,压铸件上的嵌件数量不宜过多;其次,嵌件与压铸件的连接必须牢固,同时要求在嵌件上开槽、凸起、滚花等;再次,嵌件必须避免有尖角,以利安放并防止铸件应力集中,铸件和嵌件之间如有严重的电化腐蚀作用,则嵌件表面需要镀层保护;最后,有嵌件的铸件应避免热处理,以免因两种金属的相变而引起体积变化,使嵌件松动。
压铸件壁厚的设计规范
薄壁比厚壁压铸件具备更高的强度和更好的致密性,鉴于此,压铸件设计中应该遵循这样的原则:在保证铸件具有足够强度和刚性的前提下应该尽可能减少壁厚,并保持壁厚具有均匀性。实践证明,压铸件壁厚设计一般以2.5-4mm为宜,壁厚超过6mm的零件不宜采用压铸工艺生产。压铸件壁太厚、壁太薄对铸件质量影响的表现:如果设计中铸件壁太薄,会使金属熔接不好,直接影响铸件强度,同时会给成型造成困难;壁太厚或者严重不均匀时,容易产生缩瘪及裂纹,另一方面,随着壁厚的增加,铸件内部气孔、缩松等缺陷也随之增多,同样会降低铸件强度,影响铸件质量。
压铸件加工余量的设计规范
一般情况下,由于压铸工艺的局限性,压铸件的某些尺寸精度、表面粗糙度或者是形位公差达不到产品图纸要求时,企业应该首先考虑到采用如校正、拉光、挤压、整形等精整加工的方法来进行修复,在精整加工不能完全解决这些问题时,就应该对压铸件的某些部位进行机械加工,这里要注意的是,在进行机械加工时应考虑选用较小的加工余量,同时尽量以不受分型面及活动成型影响的表面为毛坯基准面,以免影响加工精度。
压铸件脱模斜度的设计规范
设计压铸件时,就应在结构上留有结构斜度,无结构斜度时,在需要之处,必须有脱模的工艺斜度。斜度的方向,必须与铸件的脱模方向一致。
压铸机分类:
热室压铸机:锌合金,镁合金等;冷室压铸机:锌合金,镁合金,铝合金,铜合金等;立式压铸机:锌,铝,铜,铅,锡 [2] 。
热室和冷室的区别在于:压铸机的射料系统是否浸泡在金属溶液里。压铸机也可分为卧式与立式 [3] 。
压铸金属材料:
主要压铸用合金材料有锡、铅、锌、铝、镁、铜等。以锌、铝合金应用最广,镁、铜合金次之。当前在电子行业用的以锌,铝,镁合金为主。
压铸锌合金
锌合金的熔融状态流动性非常好,熔点低只有365度。可进行各种后加工处理,比如电镀等。所以用途广泛,之前在手机行业也使用很多,但因为比得大,耐蚀性差渐被铝合金淘汰。使用最多的当属卫浴行业。常用的有2,3,4,5,7号合金,最广泛的是3号合金。
压铸铝合金
铝合金密度低,但强度比较高,接近或超过优质钢,塑性好,可加工成各种型材,具有优良的导电性、导热性和抗蚀性,工业上广泛使用,使用量仅次于钢。铝合金的比重量只有铁的约1/3,所以在各行各业中用途十分重要,尤其是在飞机,船舶,汽车,电子仪器等的轻量化过程中发辉不可或缺的作用。
常用的有Al-Si-Cu系,常见的有ADC12(A383),ADC10(A380)等。另外还有Al-Si系,Al-Si-Mg系,Al-Mg系。另称作铝钛合金的是在上述材料加入钛金属改良而成,加入钛金属可以显著提高产品的机械性能。
压铸镁合金
镁合金是以镁为基加入其他元素组成的合金。其特点是:密度小,比强度高,比弹性模量大,散热好,消震性好,承受冲击载荷能力比铝合金大,耐有机物和碱的腐蚀性能好。镁的比重大约是铝的2/3,是铁的1/4。所以在手机,通讯设备等电子器材,汽车配件,医疗器械上使用广泛。
使用最广的是镁铝合金,其次是镁锰合金和镁锌锆合金。使用的牌号常见的有AZ91D,AM60B,AM50A,AS41B等。
压铸模具
压铸模具必须用热作模具钢制作,常用的钢材有:H13,2344,8407,8418,SKD61,DAC,FDAC等。
模具的结构:(后模,前模)模架,模仁,导柱,导套顶针,司筒,分流子,浇口套,滑块,斜导柱,油压抽芯。
模具的加工设备:铣床,CNC加工中心,线切割(慢走丝),(镜面)火花机,磨床,车床,焊补设备。
精密铸造铸件按照材质分类:
普碳钢精密铸件、合金钢精密铸件、不锈钢精密铸件和不锈铁精密铸件
如果按照应用领域分类可分为:
汽车铸件、高铁铸件、摩配铸件、船舶铸件、卫浴铸件、锁具铸件、化工机械铸件、工程机械铸件、医疗设备铸件、气动工具铸件、钉枪配件铸件、缝纫机零件铸件
品 名:硅溶胶精密铸造
材 质:201、304、316等不锈钢材质及碳钢等各类金属材质
表面处理:酸洗、钝化、抛丸、镜面等各类金属表面处理
打样周期:4-7天左右